高速往復式枕式包裝機中鋁塑復合膜的熱封優化是提升包裝密封性、效率及產品穩定性的關鍵。以下是系統性優化方案,涵蓋材料、工藝、設備及質量控制等方面:
一、材料特性分析與選型
1、鋁塑復合膜結構優化
- 層間匹配性:確保鋁箔層(如1235鋁箔,厚度9-12μm)與塑料層(如PE、CPP或PET,厚度40-60μm)的熱封性能匹配,避免分層或熱收縮差異。
- 涂層選擇:優先選用耐高溫、低摩擦系數的涂層(如PVDC、ACA涂層),提升熱封穩定性和抗污染能力。
- 厚度均勻性:控制膜厚公差(±5%),避免局部熱封不均。
2、材料預處理
- 表面清潔:在線配置靜電消除器或毛刷輥,清除膜面粉塵或油污,防止熱封虛封。
- 預熱處理:對低溫環境(如冬季)下的膜材,增加預熱輥(溫度40-50℃)提升材料韌性。
二、熱封工藝參數優化
1、溫度控制
- 熱封溫度范圍:
- 鋁塑復合膜典型熱封溫度為180-230℃(如PE層)或220-260℃(如CPP層),需根據涂層類型調整。
- 高速包裝需適當提升溫度(+5-10℃),補償熱封時間縮短的影響,但避免超過280℃導致鋁層脆化。
- 加熱系統穩定性:
- 采用閉環溫控系統(PID+熱電偶反饋),確保溫度波動≤±2℃。
- 熱封刀表面鍍硬鉻或陶瓷涂層,減少粘連和溫度損失。
2、壓力與時間調節
- 壓力設置:
- 氣壓范圍0.3-0.5MPa,需均勻分布(通過氣囊或彈性硅膠墊緩沖),避免局部壓強過大損傷鋁層。
- 往復式機型需注意壓力同步性,避免因機械振動導致壓力波動。
- 熱封時間:
- 高速包裝下熱封時間通常為0.2-0.5秒,需結合溫度與壓力綜合調整。
- 增加冷卻定型時間(如延長至0.3秒),防止高速牽引導致封口變形。
3、冷卻系統優化
- 冷卻方式:
- 熱封后立即冷卻(如水冷輥溫度≤40℃或風冷),快速固化封口,提升封口強度。
- 避免急冷:鋁塑膜冷熱收縮率差異大,需梯度冷卻(如先空冷0.1秒再強制冷卻)。
- 冷卻板設計:
- 使用高導熱材料(如鋁合金)并鏡面拋光,減少膜材粘連。
三、設備結構改進
1、熱封刀設計
- 形狀優化:采用圓角或梯形熱封刀(R角≥1mm),減少應力集中,避免鋁層破裂。
- 表面處理:噴涂防粘涂層(如特氟龍)或鑲嵌陶瓷導條,降低封口剝離力。
- 往復式動態補償:集成位移傳感器,實時調整熱封刀平行度(誤差≤0.1mm)。
2、張力控制
- 恒定張力:通過舞輥+伺服電機系統,保持膜材張力波動≤5%,防止熱封時膜材拉伸變形。
- 分區張力:對多層復合膜,獨立控制各層張力,避免層間錯位。
3、防偽與檢測集成
- 在線監測:加裝紅外測溫儀實時監控熱封溫度,或通過超聲波檢測封口密度。
- 瑕疵標記:對漏封、燙穿等缺陷自動標記,便于后續剔除。
四、工藝穩定性保障措施
1、參數標準化
- 建立熱封參數數據庫(如溫度-壓力-速度矩陣),針對不同膜材預設工藝曲線。
2、動態補償機制
- 速度自適應:當包裝機速度提升時,自動增加溫度5-8℃或延長熱封時間0.1秒。
- 環境補償:在高溫高濕環境(如RH>70%)下,提高熱封溫度5℃并降低冷卻水溫。
3、定期維護
- 熱封刀清潔:每班次結束后用酒精擦拭熱封刀表面,防止殘留物堆積。
- 關鍵部件檢查:每周檢測加熱管絕緣性、氣壓管路密封性及冷卻輥磨損情況。
鋁塑復合膜在
高速往復式枕式包裝機中的熱封優化需綜合考慮材料特性、工藝參數、設備精度及環境因素。通過精準溫控、壓力補償、冷卻定型及在線監測,可實現封口強度提升20%-30%,同時降低廢品率和能耗。建議結合具體生產條件進行試機驗證,逐步迭代優化方案。
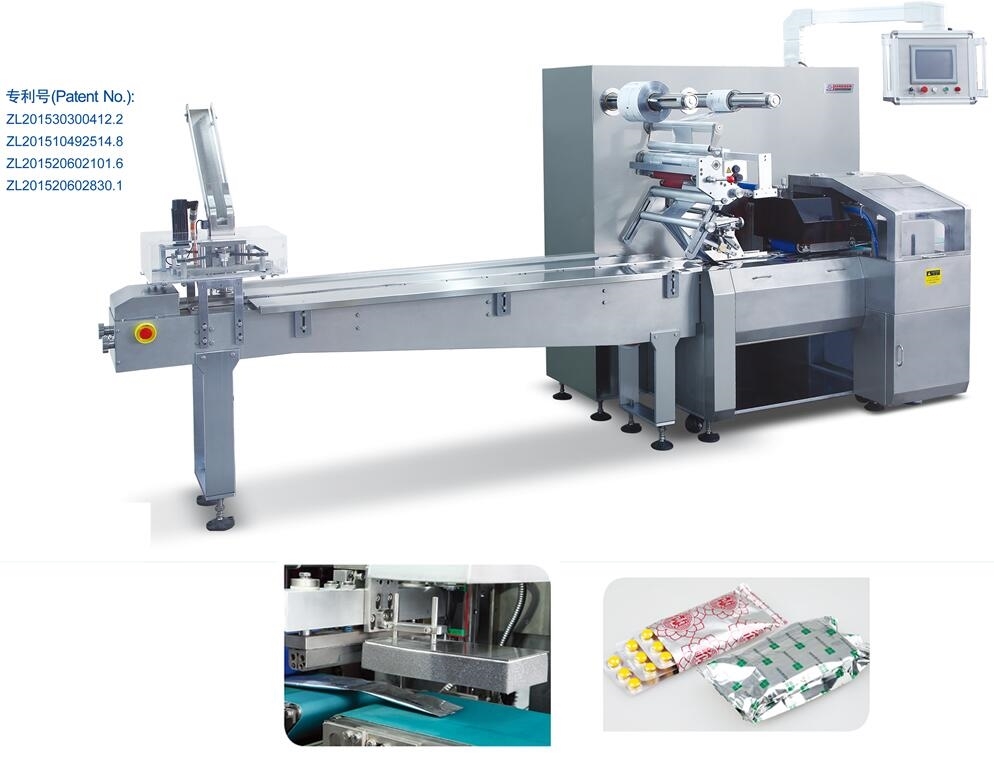